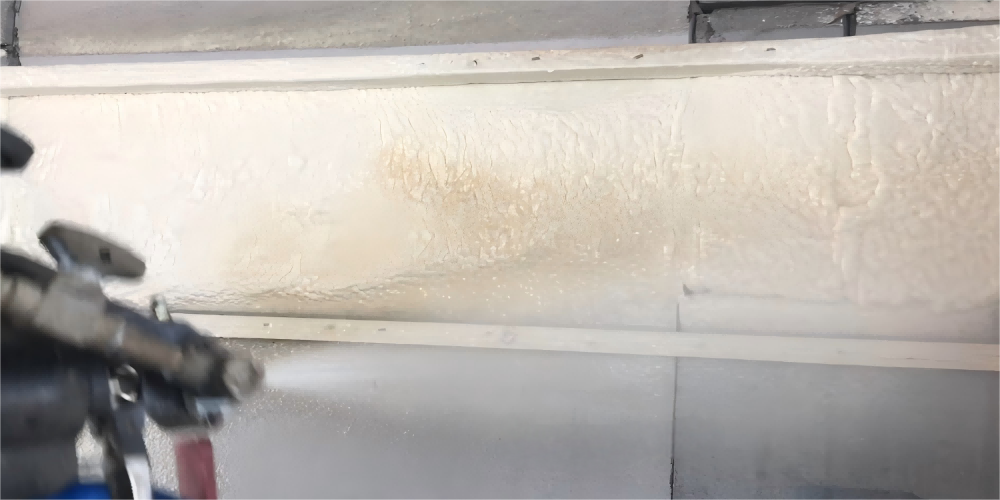
Technical points of polyurethane rigid foam spraying construction
Rigid polyurethane (PU) insulation is a polymer made by reacting isocyanates with polyols. Due to its good thermal insulation performance and excellent waterproof performance, it is widely used in external wall insulation, roof insulation, and thermal insulation of special parts such as cold storage, grain depot, archives, pipelines, doors and windows.
Polyurethane spraying technology is difficult to master, and generally in construction, it is easy to cause problem such as uneven bubble holes, and the following key technical problems need to be solved:
Control of milky time and atomization effect;
The formation of polyurethane foam goes through two stages: foaming and maturation.
Polyurethane starts from the mixing of isocyanate and blend polyol materials to the cessation of foam volume expansion, the process called foaming. During the foaming process, the uniformity of the bubble cells should be considered. The cell uniformity is mainly affected by the following factors:
1. Material ratio deviation
The density of machine bubbles and manual bubbles is quite different. Normally, the fixed material ratio of the machine is 1:1, but due to the large difference in the viscosity of the blend polyol of each manufacturer, the actual material ratio is inconsistent with the fixed material ratio of the machine. When the blend polyol is excessive, the foam density is low, the color is whitish, the foam strength decreases, the feel is soft, and it is easy to shrink when the temperature is low; When the isocyanate is excessive, it is manifested as high foam density, dark color, high foam strength, and hard and brittle feel. In these cases, the material ratio should be checked immediately to see if the filter is blocked, and whether the pressure and temperature indication are normal to ensure the accuracy of the black and white material ratio.
2. Ambient temperature
Polyurethane foaming is highly affected by temperature. When the ambient temperature is high, the environment can provide heat to the reaction system, which can increase the reaction speed and shorten the reaction time. It is manifested that the foam is fully foamed, and the density of the foam surface and core is similar.
When the ambient temperature is low, some of the heat of reaction is dissipated into the environment. On the one hand, the loss of heat causes the foam maturation period to be prolonged, and the foam shrinkage rate is increased. On the other hand, the amount of foam material is increased. The experimental results show that the foaming volume at ambient temperature of 15°C is 25% smaller than that at 25°C, which increases the production cost of foam.
3. Wind power
During spraying construction, the wind speed is required to be less than 5m/s. If the wind speed exceeds 5m/s, the heat generated by the reaction will be blown away, which will affect the rapid foaming reaction of the polyurethane foam and make the surface of the product brittle. At the same time, because the spraying foaming machine will mix the raw materials and spray them out in an atomized state, if the wind speed is too large, it will blow away the atomized particles, increase the loss of raw materials, and pollute the environment.
4. Base temperature and humidity
From engineering practice, it can be seen that the temperature of the base wall also has a great impact on the foaming efficiency of polyurethane. During the spraying process, if the ambient temperature and the temperature of the base wall of the building are very low, the reaction heat will be quickly absorbed by the base layer after the first spraying of rigid foam polyurethane, thereby reducing the foaming amount of the material.
Therefore, the noon break should be shortened as much as possible during construction, and the process should be reasonably arranged in the construction arrangement process to ensure the foaming rate of rigid foam polyurethane. Rigid polyurethane foam is a polymer product produced by the mixed reaction of isocyanate and blend polyol two-component reaction.
The isocyanate component easily reacts with water to form urea, and if the urea bond content in the polyurethane increases, the foam will become brittle and the adhesion between the foam and the substrate will be reduced. Therefore, the surface of the substrate to be sprayed is required to be clean and dry, the relative humidity is less than 80%, and there is no rust, no dust, no pollution, no moisture, and no construction is allowed in rainy days. If there is dew or frost, it should be removed and dried.
Qichen has been specializing in the production of spraying blend polyol of various systems for more than 10 years, and has been providing customers with customized products while providing various technical guidance. Welcome to consult and learn.