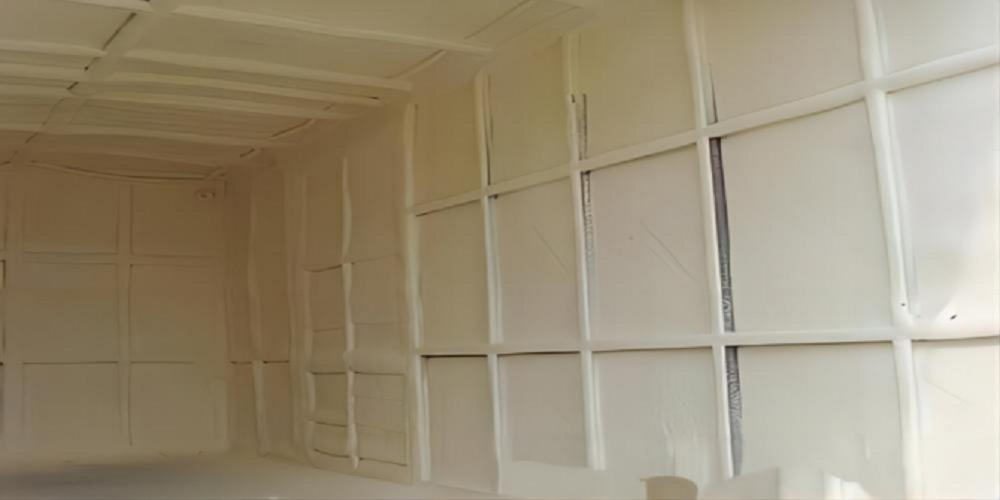
Foaming Problems, Causes and Solutions Encountered In Polyurethane Spraying Construction
1. The foam is soft.
Reason: Check the proportion of black and white material, which is generally caused by too much white material.
Solutions: It is recommended to do a free foaming test according to the correct proportion; If it is soft, the proportion of black material can be appropriately increased; If it is still soft, it is necessary to check whether the amount of amine ether (that is, polyether with ethylenediamine as the starting agent) should be appropriately increased in the raw material used in the white material.
2. The foam is crispy, and the bubble cells generally relatively thick at this time.
Reasons: Excessive moisture content in the system. If only the surface part is crispy, consider whether the difference between the material temperature and the ambient temperature is too large, the material temperature is high, and the ambient temperature is low. Another reason is that the difference in viscosity of black and white materials is too large, and there are more excess black materials.
3. The foam falling off.
Reasons: The surface of the substrate is not clean, there is floating ash or oil; The substrate is not penetrated, and this peeling is visible to the moisture of the interface; In addition, the substrate temperature is too low and the foaming speed is too fast; There is no "priming" (i.e., a thin layer is sprayed first), but a thicker spray at one time can also cause excessive tension and peeling.
4. The foam cracking or heartburn, the cracked gap can be clearly seen on the site.
Reason: The low branching degree and functional of polyether used in the foaming system.
Solutions: Polyether with sucrose, mannitol and sorbitol as the starting agent can be appropriately added. In addition, the number of spray coatings is appropriately increased during construction to avoid the phenomenon of starting at one time.
5.The foam surface bulging. This phenomenon occurs as soon as the spray is completed sometimes,and occurs after several hours sometimes. The serious ones will bulge one by one larger "package".
Reasons: The type of foaming agent in the foaming material is incompatible with the system, and the second foaming is accumulated after the foaming is completed.
Solutions: The foaming agent should be used in conjunction with polyether and additives, and the best solution to encounter this phenomenon at the construction site is to appropriately increase the number of foaming layers and reduce heat accumulation.
6.The foam shrinkage. Sometimes it is local contraction, and sometimes it is overall retraction.
Reasons: The foam density is too small, the water content is too large, resulting in the imbalance of the proportion of black and white materials; Another reason is due to too low temperature; Uneven mixing of the machine is also a factor in local shrinkage.