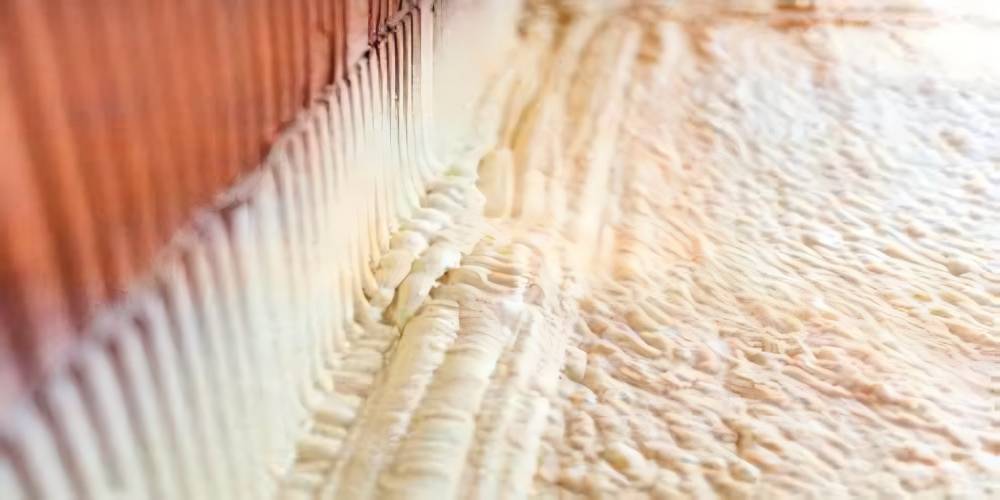
Issues and sloutions when applying polyurethane rigid foam
Polyurethane rigid foam is a kind of foam plastic formed through a rapid chemical reaction between blended polyol and isocyanate mixed in a specfic proportion.It possesses excellet waterproofing, thermal insulation and heat preservation capabilities.
There’re several issues that may arise when using polyurethane rigid foam? What’s the reason and how to solve them ? Let’s hear the advice from our technical team.
1: Foam shedding
Cause: The low temperature of the sprayed surface or excessive humidity in the air causing moisture on the sprayed surface can reduce the adhesion between the foam and the surface, leading to easy shedding of the entire foam piece.
Solution:
a: If constructing on rainy days with high humidity, find ways to dry the sprayed surface;
b: If constructing on days with low temperature, heat the raw materials. If possible, preaheat the sprayed surface
c: If necessary, increase the proporation of isocyanate or decrease the proportion of blended polyol to accelerate the reaction and improve the adhesion.
2: Foam Shrinkage
Cause: Foam shrinkage refers to the phenomenon where the foam contracts around its edges after formation, creating large gaps between it and the sprayed surface, which affects bonding strength and sealing and can easily lead to shedding. This is caused by increased viscosity and reduced fluidity of the materials during construction under low temperatures, resulting in volume contraction during foam formation.
Solution: Heat the raw materials and surroundings, and appropriately increase the air flow rate to ensure uniform mixing of the materials and accelerate the reaction speed.
3: Dead Foam
Cause: Dead foam refers to foam that is too dense or does not foam at all. This is due to insufficient foaming agent in the raw materials or low temperatures.
Solution: During construction at low temperatures, heat the raw materials, increase the air volume, adjust the formula, and increase the use of catalysts and foaming agents to shorten the reaction time.
If dead foam occurs during construction at normal temperatures, it may be due to prolonged storage of blended polyol, causing the foaming agent to volatilize. In this case, add some foaming agent.
4: Brittle Foam
Cause: Improper raw material ratio, with too much isocyanate used.
Solution: Appropriately reduce the flow rate of diisocyanate to decrease its usage.
5: Soft Foam
Cause: Improper raw material ratio, with low ratio of isocyanate used.
Solution: Simply increase the amount of isocyanate or decrease the amount of blended polyol.