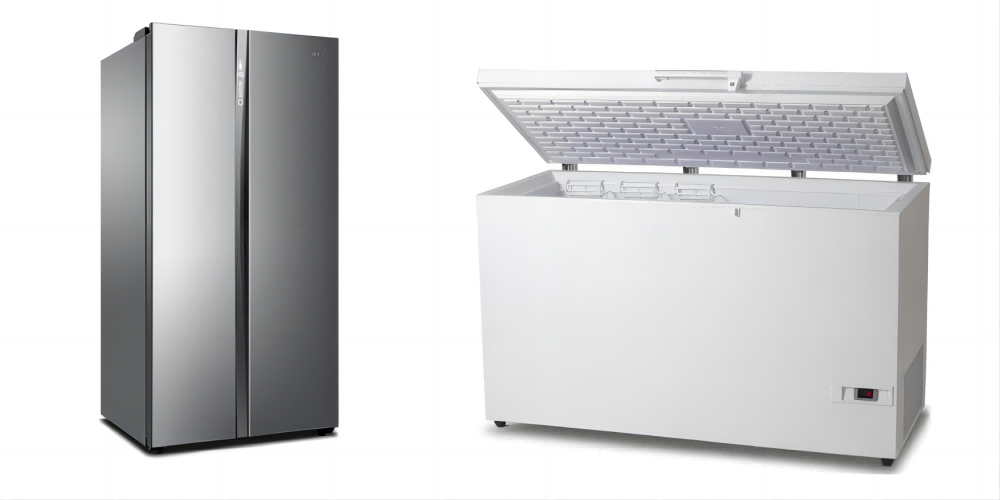
Analysis of common problems in refrigerator and freezer foaming
Polyurethane rigid foam with thermal insulation effect is widely used in refrigerators and freezers, but there are many problems encountered in the foaming process, and the following is the analysis of some common problems:
1. Causes of the spill
1. The filling amount of foaming material is excessive, which is mainly manifested as high foam core density.
2. The viscosity of the raw material is too low or the reaction speed is too slow.
3. The mixing is uneven.
4. The proportion of black and white materials is too low, and the density of free bubbles is low.
5. The content of foaming agent is too small, and the free bubbles density is low.
6. The box is not well sealed.
7. The mold temperature and material temperature are not within the specified range.
2. Causes of the shrinkage of the foam
1. The black and white materials are mixed unevenly, the local white materials are too much, and the foam is soft.
2. The filling amount of foaming material is small, which is mainly manifested in the low density of the foam core.
3. The ratio of black and white material is wrong, there are more white materials, and the density is low.
4. The amount of foaming agent is too much, and the free bubbles density is low.
5. The demoulding time is too short.
3. Causes of the delamination of the inner tank or shell with the foam
1. The mold temperature is too low.
2. The demoulding time is too short.
3. The adhesion between the material and the foam is poor.
4. The surface of the inner tank or side plate is contaminated.
4. Causes of demoulding expansion
1. The filling amount of foaming material is excessive, which is mainly manifested as high foam core density.
2. The content of foaming agent is too much, resulting in a low density of free bubbles and a large expansion coefficient.
3. The demoulding time is too short, and the degree of curing is not good.
4. The proportion of black and white material is too low, the density of free bubbles is low, and the expansion coefficient becomes larger.
5. The mold temperature is too low, which affects the curing speed of the foam
6. The temperature of the raw material is too low, which affects the curing speed.
7. The mold is not pressed well or the inner tube air pressure is insufficient.
5. Causes of foam cavities or cavitations
1. The filling amount of foaming material is insufficient, which is mainly manifested in the low density of the foam core.
2. The proportion of black and white material is too high, the density of free bubbles is high, and the fluidity becomes poor.
3. The temperature of raw materials is too high or too low, which affects the fluidity.
4. The mold temperature is too low or too high, which affects the fluidity.
5. The black and white material is not mixed well, and the injection pressure of the black and white material is unstable.
6. The exhaust hole is not well set, and the exhaust hole is increased according to the flow direction and the end mixing surface
7. The content of foaming agent is too small, resulting in high density of free bubbles and poor fluidity.
Qichen is a manufacturer specializing in the production of Blended Polyol for refrigerators, freezers, plates, building walls and roofs , etc., Qichen is committed to providing customers with customized raw materials and solving a series of technical problems at the same time.